Negli ultimi giorni si è parlato molto del Titan e della sua tragedia che ha portato alla morte di 5 persone. Come sempre, del senno di poi sono piene le fosse e se ne sono sentite di ogni. I giornalisti (o giornalai?) si sono scatenati alla ricerca di chiunque per un’opinione e tra questi è saltato fuori James Cameron, professione regista, che ha detto la sua qui. In particolare afferma che
Non ho mai creduto in quella tecnologia di fibra al carbonio avvolta, di filamento avvolto, di scafo cilindrico
LA FIBRA DI CARBONIO
La fibra di carbonio è un polimero di soli atomi atomi di carbonio che si presenta in sottilissimi fili che vanno da 5 a 15 micron.
La fibra di carbonio è come un tessuto e quindi non riesce a mantenere una forma precisa ma, impregnandola in apposite resine prima e polimerizzando il tutto poi, si ottiene un manufatto con la forma voluta. Una volta completato il processo si ha un materiale con una massa volumica circa un quarto dell’acciaio (2200 kg/m3 contro 7850 kg/m3) ma con caratteristiche meccaniche doppie (resistenza a trazione a partire da 2000MPa contro i gli 800/1000MPa degli acciai più comuni).
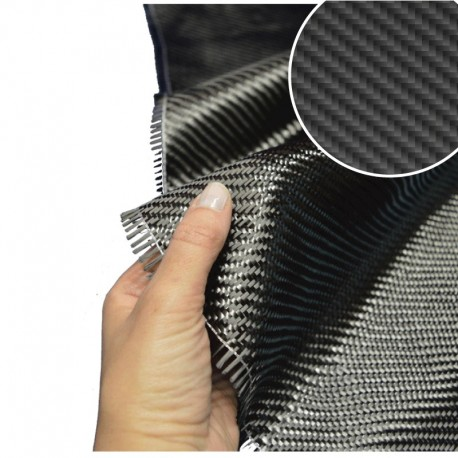
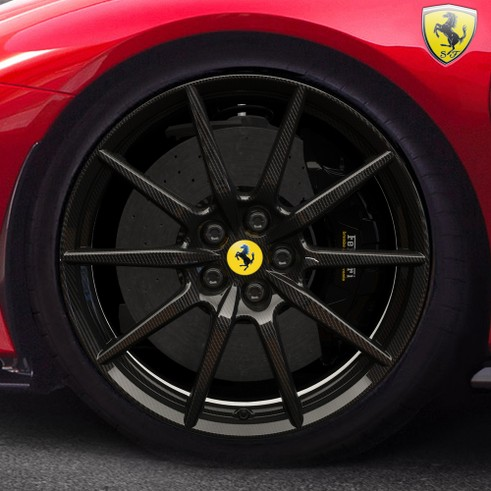
Una delle differenze principali del composito a fibra di carbonio rispetto all’acciaio è quello di avere un comportamento anisotropo cioè reagisce alle sollecitazioni in maniera differente in base a come viene caricato. Questo è dovuto all’orientamento della trama dei filamementi, ragion per cui deve essere accuratamente studiato in fase di progettazione per garantire le prestazioni meccaniche desiderate.
Altra grossa differenza rispetto agli acciai comuni è la sua elevata resistenza agli agenti chimici pertanto la sua ossidazione è nulla in ambiente marino (dove, al contrario, gli acciai sono nella fossa dei leoni…) e la sua scarsa conduttività termica.
Il composito in fibra di carbonio è utilizzato nel settore aerospace da Boeing e da Airbus che hanno realizzato rispettivamente il 787 e A350XWB con fusoliera e parti strutturali in composito e senza rivettature. Nel settore automotive da tempo le vetture di formula 1 e le moto da competizione hanno parti in carbonio. Addirittura Alfa Romeo ha realizzato sulla 4C un telaio monoscocca in composito con massa di soli 65kg!
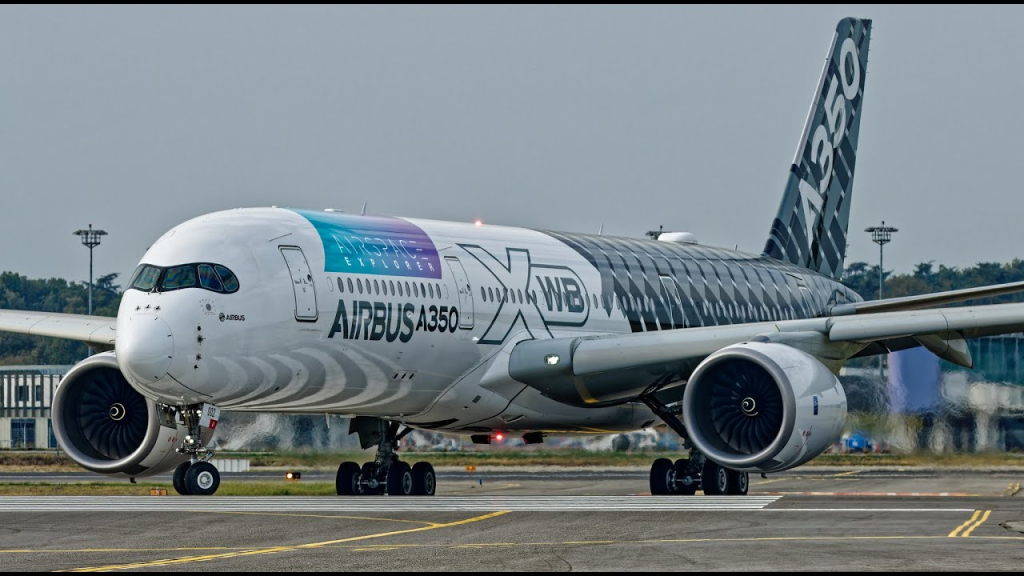
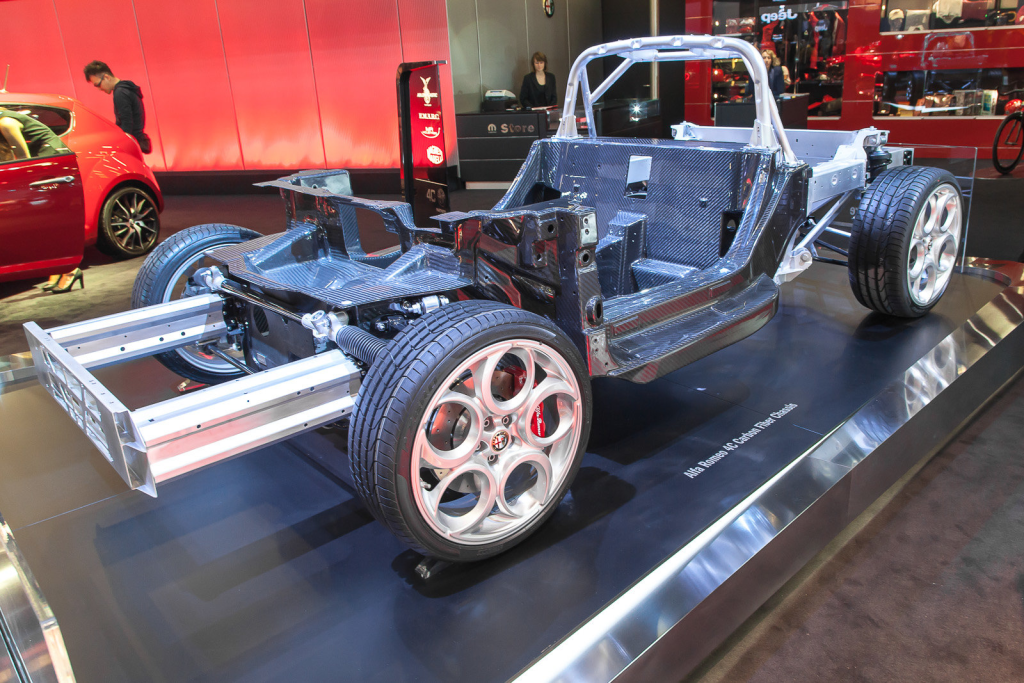
IL FENOMENO DELLA FATICA
Uno dei problemi che affligge tutti i materiali è quello della fatica. Per capire questo fenomeno basta prendere un fermaglio e piegarlo più volte: dopo un certo numero di “cicli” si rompe.
Questo avviene perchè il materiale, sottoposto a cicli di lavoro, degrada le sue caratteristiche meccaniche per giungere a rottura a carichi ben inferiori a quelli teorici. Questo fenomeno venne studiato quando, verso la fine dell’800, si presentarono delle inspiegabili rotture sugli assili ferroviari con le catastrofiche conseguenzale che ne derivavano. Pertanto la progettazione degli organi meccanici che sono sottoposti a cicli di lavoro viene effettuata sempre a fatica dove il carico di rottura teorico del materiale, per effetto della fatica, diventa anche inferiore a 1/10 di quello statico. Ma perchè si verifica questo fenomeno?
Il materiale subisce localmente delle sollecitazioni superiori a quelle in grado di supportare e si danneggia. Da li si innesca il fenomeno che, dopo milioni di cicli, porta alla rottura del componente.
Per sapere qual’è il limite si costruisce la curva di Wholer o curva S-N: questa è derivata da test di fatica ad alto numero di cicli applicando un carico ad ampiezza costante (secondo la DIN 50100), ed è divisa in aree: fatica a basso numero di cicli K, vita a fatica finita Z e fatica ad alto numero di cicli D . Le tre aree sono limitate dai numeri di cicli N.
- Fatica a basso numero di cicli, 100-30.000 cicli: la fatica a basso numero di cicli K è al di sotto dei 104 – 105 cicli di carico. La resistenza alla fatica a basso numero di cicli viene determinata con la prova di fatica a basso numero di cicli (LCF). I materiali ed i componenti sono sollecitati al punto che durante il ciclo si verificano deformazioni plastiche e il materiale cede in fase iniziale. Per una rappresentazione più dettagliata, spesso viene utilizzato il modello Coffin-Manson. Un carico che porta alla rottura del provino entro un quarto dei cicli, viene definito come resistenza statica, determinata anche con una prova di trazione.
- Vita a fatica finita, 2.000.000 cicli circa: la vita a fatica finita Z è l’intervallo tra 104 e 2×106 cicli (a seconda del materiale), dove il provino raggiunge sempre una condizione di criterio di cedimento (per esempio cricca o rottura). La resistenza a fatica a vita finita viene determinata con la prova di fatica ad alto numero di cicli (HCF). Dopo la prova, il risultato è il numero di cicli di carico ad una determinata ampiezza di carico.
- Fatica ad alto numero di cicli, cicli infiniti: la fatica ad alto numero di cicli D indica il limite di tensione che un materiale può sopportare durante il carico ciclico senza significativi segni di fatica o cedimento. Nell’area della fatica ad alto numero di cicli, si stabilisce un numero limitato di cicli NG . Se il provino non resiste prima di raggiungere questo numero limitato di cicli, viene considerato come “cedimento”. I materiali che, durante una prova di fatica ad alto numero di cicli, sopportano più di 1.000.000 di cicli senza rottura sono considerati resistenti alla fatica. Il concetto di fatica ad alto numero di cicli comporta sollecitazioni ammissibili significativamente inferiori rispetto al concetto statico.
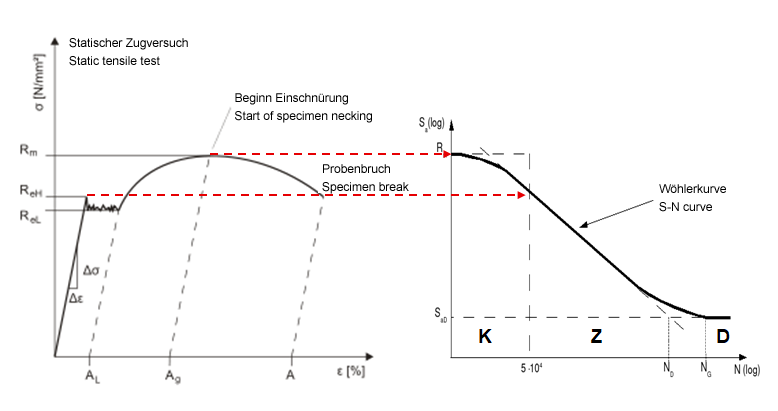
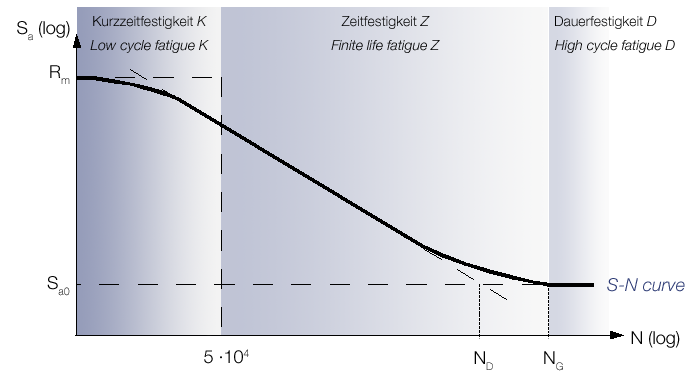
Negli organi di macchina e più generalemente nelle strutture spesso i parametri di forma, le tipologie dei vincoli le forme di applicazione dei carichi sono diversi da quelli ipotizzati. Sotto queste nuove condizioni nascono delle concentrazioni locali di sforzo che costituiscono l’ effetto d’intaglio o di forma. per fare qualche esempio influiscono
- i fori su piastre o dischi;
- le saldature;
- le cave per chiavette;
- gli accoppiamenti forzati;
- le filettature;
- le gole;
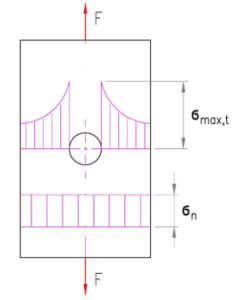
Un esempio disastroso della scarsa conoscenza di questo fenomeno fu il comet, primo aereo di linea commerciale pressurizzato costruito attorno agli anni ’50 e che subì una serie di incidenti a distanza ravvicinata ovvero in meno di 2 anni dalla presentazione subì 3 incidenti con 99 vittime che portarono le autorità alla revoca della licenza di volo. Come tutti i disastri ovviamente partirono le indagini e per tentare di capire le cause di questi incidenti decisero di effettuare dei test di pressurizzazione delle fusoliere per i modelli esistenti mediante un enorme serbatoio d’acqua. il risultato fu che rispetto ai 16000 cicli di progetto la fusoliera presentava cedimento a fatica dopo poche migliaia se non addirittura centinaia di cicli.
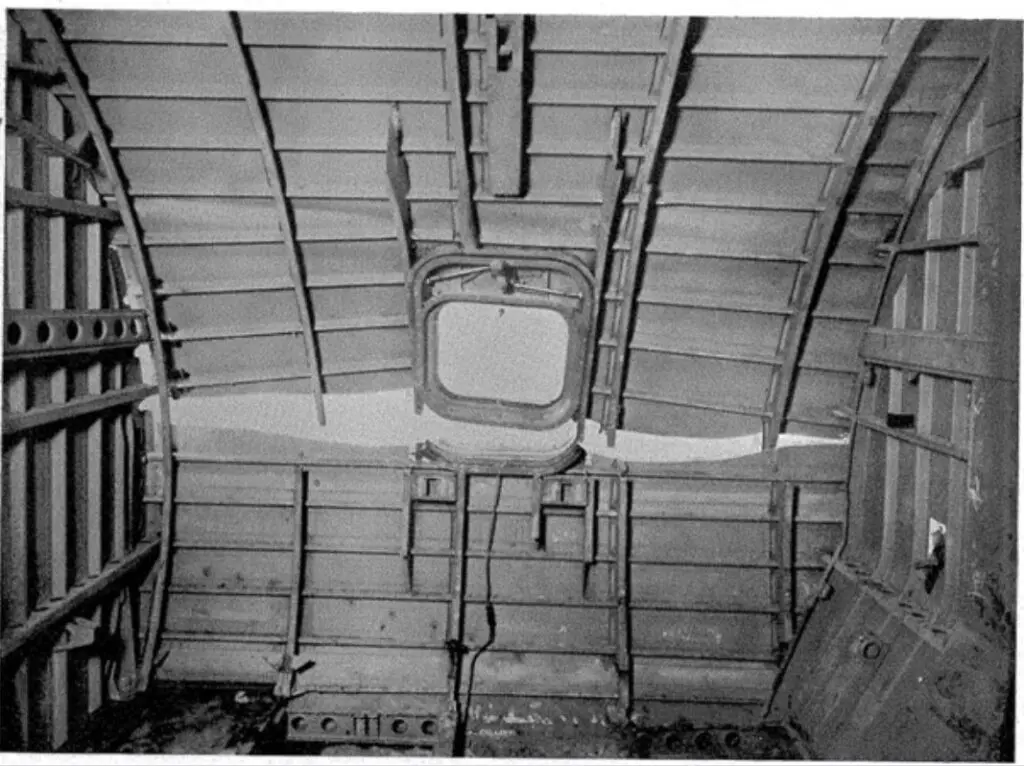
L’eccessiva pressurizzazione della fusoliera provocò lo snervamento del materiale in prossimità degli angoli dei finestrini a forma quadrangolare, i quali rappresentavano delle zone di concentrazione degli sforzi. Lo snervamento degli angoli comportava l’incrudimento del materiale, ovvero il rafforzamento che si ha in presenza di una deformazione plastica (permanente), e di conseguenza un miglioramento delle sue proprietà meccaniche, fra cui anche la resistenza a fatica. Questo processo di rafforzamento per snervamento da sovrapressione prende il nome di autofrettage e viene utilizzato consapevolmente tutt’ora per migliorare la resistenza meccanica statica e a fatica di contenitori in pressione. Grazie alle verifiche condotte in seguito agli incidenti si determinò che la cricca generata dalla sollecitazione a fatica cresceva preferenzialmente a partire dagli angoli dei finestrini di forma quadrangolare che caratterizzavano il Comet. Questo accadeva perché la forma squadrata del finestrino aumentava l’effetto di concentrazione degli sforzi dovuti alla presenza stessa del finestrino nella fusoliera.
Ad oggi, il problema è stato risolto arrotondando la forma dei finestrini per ridurre l’effetto di concentrazione degli sforzi in modo da sfavorire la nucleazione di cricche.
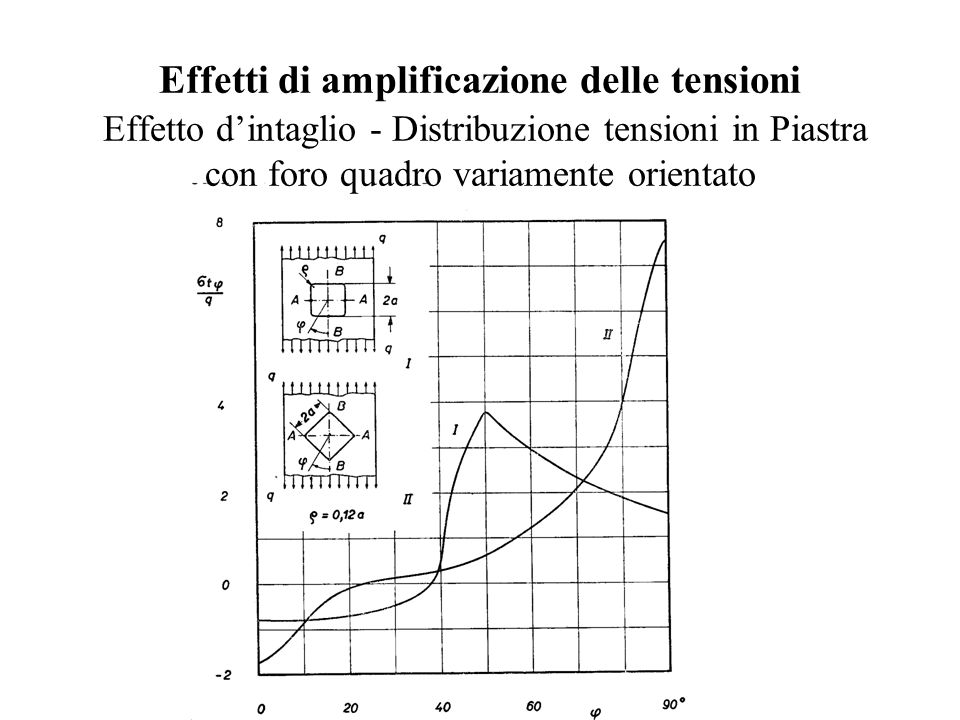
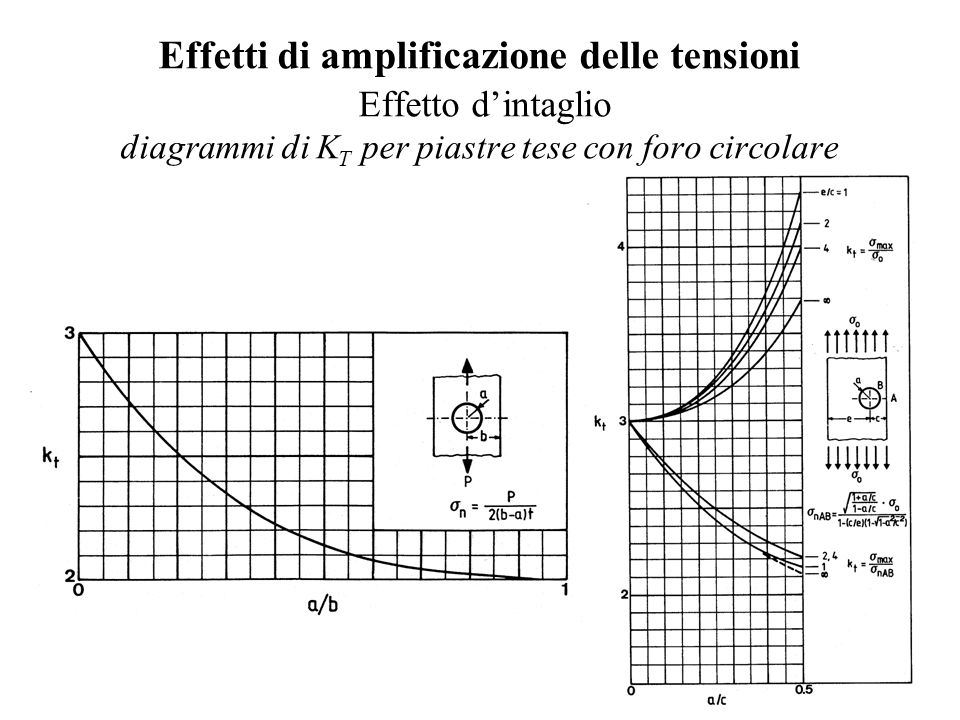
FATICA NEI COMPOSITI
Similmente a quanto avviene nei materiali metallici, l’applicazione ad un composito di carichi
variabili ciclicamente può dar luogo a rottura anche quando la massima sollecitazione risulta
inferiore alla resistenza statica del materiale (fatica). Nei compositi, similmente a quanto accade nei materiali isotropi, la rottura per fatica è una rottura progressiva che si manifesta con la formazione e propagazione di difetti. Il fenomeno è comunque ben più complesso di quello osservato nei materiali metallici e può essere causato da
- scollamento fibra matrice (debonding);
- fessurazione della matrice;
- rottura della fibra;
- scollamento delle lamine (delaminazione).
La resistenza a fatica dei materiali compositi dipende da vari fattori legati alla intima natura e struttura del materiale nonché alle particolari condizioni di sollecitazione ed ambientali. Fissate le caratteristiche delle fibre, la resistenza a fatica di un composito dipende essenzialmente da:
- materiale della matrice;
- orientamento delle fibre e sequenza di impacchettamento;
- percentuale in volume di fibre;
- adesione fibra-matrice;
- tipologia di sollecitazione;
- tensione media;
- frequenza di applicazione del carico;
- condizioni ambientali (umidità, corrosione ecc).
- effetti di intaglio
L’IMPLOSIONE DEL TITAN
L’implosione è il fenomeno contrario all’esplosione: all’interno del corpo cavo, per diversi motivi, si viene a creare una pressione minore rispetto a quella esterna che farà si che il fluido esterno eserciterà una forza sulla superficie esterna del corpo, causando un collasso.
La superficie esterna del Titan era caricata, secondo la legge di Stevino (la pressione esercitata da un fluido incomprimibile a una profondità h è pari al prodotto della densità del liquido per l’accelerazione gravitazionale per la profondità stessa), a 3850m (la profondità del Titanic) da un carico statico pari a:

Oltre a questo vanno sommate le componenti dinamiche generate dalle correnti e dal movimento stesso dello scafo nel fluido.
Scoprire perchè è imploso senza poter analizzare i resti vuol dire restare solo nel campo delle ipotesi. Di sicuro possono aver giocato i fattori sopra riportati dovuti a una progettazione errata (non sono stati considerati alcune variabili e/o sono state sottistimate), non è stata fatta una accurata verifica dei materiali per prevenire fenomeni di fatica ma la cosa che più lascia perplessi è come il piccolo Titan abbia potuto effettuare attività commerciale in completa assenza di certificazioni, mettendo a rischio la vita di tutti i suoi passeggeri.